By: Zack Smith & Allan Evora, Affinity Energy
ATS MULTI-CIRCUIT METERING HELPS EFFECTIVELY MANAGE LOAD CREEP
Emergency Power Supply Systems (EPSS) are the critical infrastructure that supports a hospital system during power outages. Regulations place a lot of emphasis on testing and maintenance of the EPSS system; however, all the maintenance in the world will do no good if the EPSS becomes overloaded.
EPSS experience load creep like normal power systems. Additionally, they run the risk of reduced capacity due to the addition of non-essential loads plugged in to designated red receptacles during extended outages. These loads may consist of diagnostic equipment or in some cases “comfort equipment” such as microwaves, heaters or coffee pots. Education and training can help ensure only approved loads are plugged in to EPSS.
Submetering is the only way to truly manage load creep and prevent EPSS overload.
YOU CAN’T MANAGE WHAT YOU DON’T MEASURE
The best way to manage your capacity is to submeter your loads. For some hospitals, this is easier said than done. While you may have submetering information at the generator switchgear or even downstream submetering at EPSS distribution switchgear, the ideal location to submeter for managing load creep is the load side of the automatic transfer switch (ATS).
Newer ATSs (installed within the last 10 years) either have digital controllers that incorporate submetering as an option, or engineers had the foresight to specify that OEMs install a separate third party submeter with the ATS. Unfortunately, older ATSs need to retrofit submeters to be able to measure the ATS load. This can be a costly proposition when considering hardware and installation costs. The combination of OSHA regulations, and the fact that the ATS is part of critical infrastructure, can make modifying equipment challenging.
A COST-EFFECTIVE ALTERNATIVE TO CONVENTIONAL CIRCUIT MONITORING
Within the last five years, a new type of electrical submeter has emerged and is an ideal solution for retrofitting ATSs with submetering capability. This meter type is referred to as the multi-circuit or multiple circuit meter. The concept is simple: Use one submeter CPU/circuit board to measure multiple loads.
A multi-circuit meter has only one set of inputs for a common voltage source, and multiple sets of current inputs for loads that share the common voltage source. Due to limitations on current transformer (CT: the instrument that provides current input to the meter) lead wire length, the multi-circuit meter is best suited for loads in which the CT installation locations for the loads are near one another (typically within 100 ft.).
Examples include: submetering all the circuits within a distribution panel, or all the distribution panels within an electric room, or feeder breakers on a unit substation. Since ATSs tend to be concentrated in electric rooms and typically share a common normal and emergency voltage source, they are great candidates for multi-circuit submeters.
What makes multi-circuit submetering so cost effective? The lower hardware and installation costs. Additionally, since there is only one CPU/circuit board, there is only one low-voltage communication connection.
Our general rule of thumb: whenever you have more than two loads to submeter that meet the criteria for multi-circuit metering, go with multi-circuit metering. Its costs will be lower when compared to individual meters.
MULTI-CIRCUIT SUBMETER HARDWARE
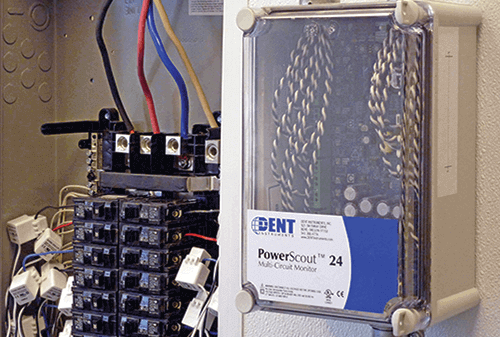
The DENT Instruments PowerScout 24 is a great example of an inexpensive yet accurate submeter that provides all the measurements necessary for monitoring ATS loads. DENT Instruments was one of the first companies to introduce the multi-circuit design.
The PowerScout 24 comes with its own enclosure, is powered via the voltage source and easily integrates to your SCADA or building automation system via Modbus or BACNet. It can measure up to 8 3-phase loads. List price for a PowerScout 24 with serial communication is $1,200. A DENT PowerScout 3037 (the single circuit meter version) is $400.
Taking in to account installation costs, it is easy to see how the multi-circuit meter is a cost-effective solution when you need to meter more than two loads that meet the multi-circuit criteria. The cost savings are even more substantial as the number of loads increases. A fully provisioned PowerScout 24 will have approximately 66% lower hardware costs when compared to individual meters. Taking in to account labor savings, the total costs savings can be as much as 80-90%.
TURN THAT DATA INTO INFORMATION
Submeters provide data. To make this data valuable, it needs to be turned into actionable information. To accomplish this, we recommend a few additional steps.
First, we recommend that submeter data be recorded. To be of benefit, the load profiles need to be analyzed over time using trending software within your SCADA or building automation system. If you don’t have an existing system, there are some very cost effective data logging devices that can store a large amount of interval data. This data can generally be exported and analyzed with a desktop application such as Microsoft Excel. We also recommend that the ATS switch position and generator run status also be recorded.
Using this information, it would be easy to analyze the data to check the load prior to the ATS switching to emergency, the load while on emergency, and the load after the ATS returns to the normal source. Using this analysis, it’s easy to identify loads added during a power outage and not removed when normal power is restored.
Another easy way to spot load creep is to trend year over year load growth. Using this analysis technique, load creep is easy to quantify.
Ultimately, multi-circuit submeters are an easily installed, inexpensive way for healthcare facility managers to conduct accurate load profiling and analysis.
ABOUT AFFINITY ENERGY
Affinity Energy is a vendor-neutral control systems integrator with a national portfolio of over 800 power automation projects and a rich depth of expertise working with mission critical facilities, distributed generation plants, energy companies, engineering firms, and construction contractors who seek open, turnkey systems for power management and energy optimization.
Specifically, they work to design, build, implement, and support controls, instrumentation, and monitoring systems, during the design and/or build phases of a new construction or retrofit project for utility-scale solar farms, airports, waste-to-energy plants, data centers, medical campus central energy plants, and manufacturing companies.
See the original post on the Affinity Energy website here.